I wanted to update with the latest mold making that’s been going on here. First of all, I finally made a mold of Nefarious’s creation “Tippy Pig”, who as I’ve mentioned before got his name due to his large head which regularly causes him to tip forward. On the left are two painted examples, cast in two slightly different plastic polymers, and painted with two different kinds of paint (Citadel and Vallejo) because I’ve been trying to figure out which paint works best on these plastics. Paint does not stick too well without a primer (and on these it’s made worse because there seem to have been quite a few bubbles — I’d love to get a vacuum chamber set up but it’s costly). The white pig is unpainted plastic, and the gray pig is an experiment in casting it using Apoxie Clay, which is a two part clay that hardens to rock-hard over a few hours without cooking. I like it a lot, and also got some similar Milliput clay that I still have to try, and although it’s intended for modeling, it did work nicely in the mold as well. After it hardened, I also experimented with adding a few changes, also using the clay, including tusks, a hat, and a big belly. Another reason I like working with it is that it’s completely bulletproof, unlike Sculpey, which I normally use, which can easily break when you’re working on it as it’s so fragile.
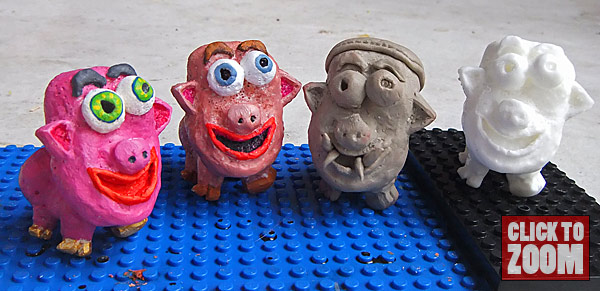
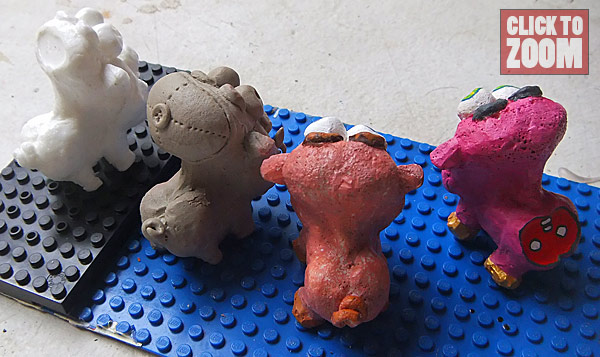
Pretty cool that Nefarious can claim to be a “real” toymaker at age seven. You may have noticed that the one pig is missing his butt and another is missing the top of his head. That’s my fault, as I didn’t pour enough plastic into the mold. But I think it turned out alright nonetheless. Caitlin is planning to paint the one with the flat head and she’s got the very good idea of mounting some fur there for a troll-esque hairdo.
I also finally made the mold for my new light switch design for double switches, and then painted it using the Vallejo paints. The tentacles are textured with ridges so it was really easy to get a pretty nice paint job by dry brushing it. The plastic I used was an ultra hard “onyx” black polymer, so it took a few coats of white and looks a little amateur. In a more motivated perfect world I think I’d cast the tentacles and the shattered switchplate as separate pieces so that I could cast each with its own colour.
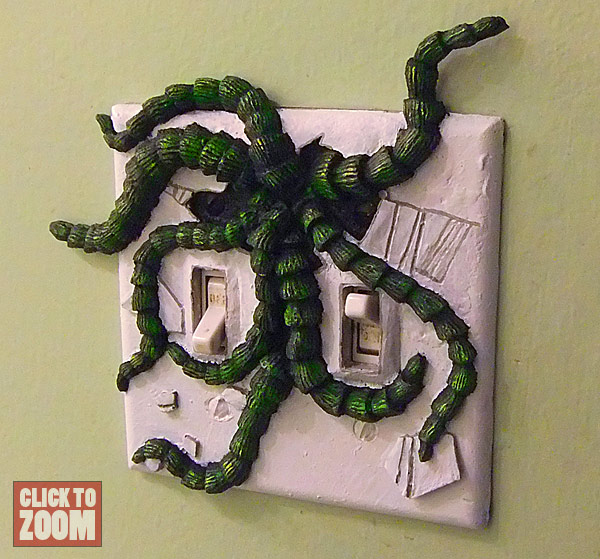
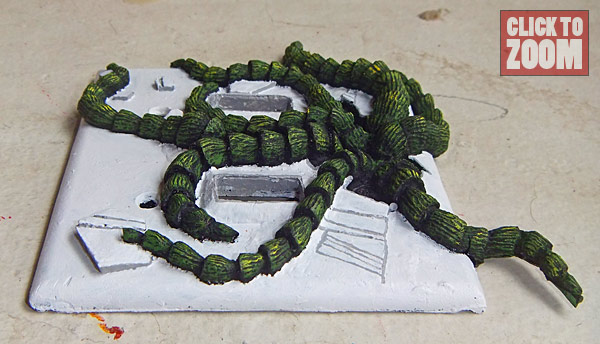
The back of course has a little credit and signature engraved in it, with the grooves filled in with silver paint. You can see where I ground off the fill spout and air-release vents. Unfortunately my hand slipped when I was doing that and it did some minor damage, but I’m not terribly upset about that.
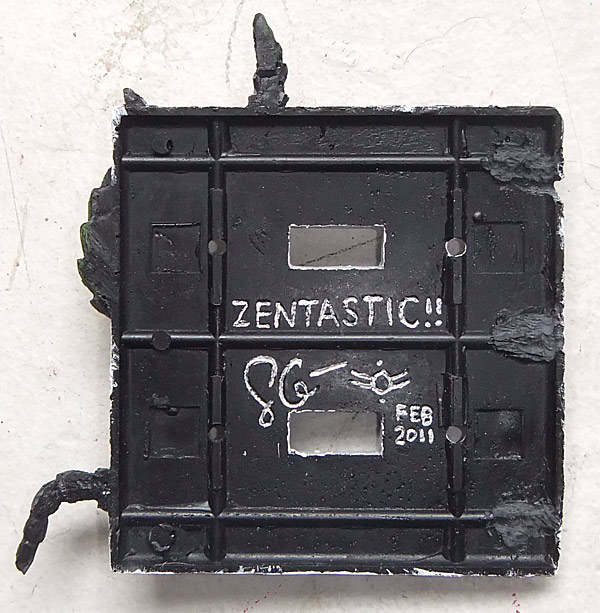
I made this ages ago but only recently made the mold. For some reason it was a bit of a pain to cast, but since the mold is “deep” in design, with the front face sitting in a fairly indented hole, in the end it was actually easier to just pour a bunch of plastic into the clear half and then as it started to harden pushing the back half (the yellow part) into it. I suppose that using that method I could have done without the spouts, so I’m going to keep that in mind for the future.
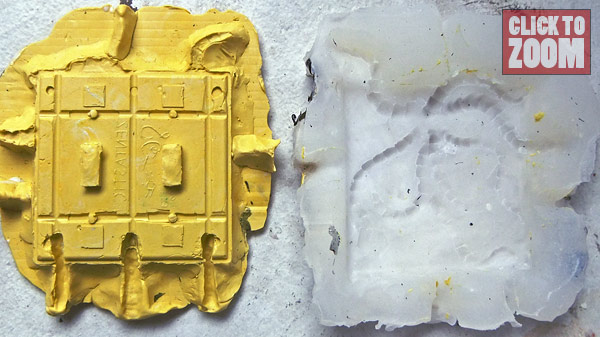
Well, I think I’m going to take a short break from making stuff and switch to programming. I’ve been avoiding it in part because the documentation for this watch is so non-existent (basically all you can do is read other people’s source code to figure it out) that I’m sure it’s going to be a little trial-and-error figuring out how to make it do neat stuff. But, it doesn’t look too hard, so I’m sure once I get over the initial learning curve that it’ll come fast. By the way, that mistake medication is finally out of my system and I’m feeling much better, so I’m hoping for a much nicer weekend than last. Fingers crossed.